1.①储运车间中间原料罐区,在可能发生硫化氢中毒的主要出入口设置危险危害因素告知牌、警示标志。
②按不同品种的原料油绘制沿工艺流程的硫化氢分布图。
③及时制订相应的岗位操作规程或操作法。
④建立健全储运车间中间原料罐区安全监测监控体系。
⑤对罐区设置的探测器及时进行维护保养。
⑥应急救援防护器材根据车间、工段实际需要进行合理配备。
⑦公司和车间定期组织开展全员安全教育培训。
2.LOPA分析基本程序
①场景识别与筛选。(严重的事故场景)
②初始事件确认。(偏差产生的原因)
③IPL评估。(独立保护层评估)
④场景频率计算。(场景的风险)
⑤评估风险,作出决策。
⑥后续跟踪和审查。
LOPA分析基本程序
(1)场景识别与筛选。LOPA通常评估先前危害分析研究中识别的场景。分析人员可采用定性或定量的方法对这些场景后果的严重性进行评估,并根据后果严重性评估结果对场景进行筛选;
(2)初始事件确认。首先,选择一个事故场景,LOPA一次只能选择一个场景;然后确定场景IE。IE包括外部事件、设备故障和人员行为失效;
(3)IPL评估。评估现有的防护措施是否满足IPL的要求是LOPA的核心内容;
(4)场景频率计算。将后果、IE频率和IPL的PFD等相关数据进行计算,确定场景风险;
(5)评估风险,作出决策。根据风险评估结果,确定是否采取相应措施降低风险。然后,重复步骤(2)~(5)直到所有的场景分析完毕;
(6)后续跟踪和审查。LOPA分析完成后,对提出降低风险措施的落实情况应进行跟踪。应对LOPA程序和分析结果进行审查。
HAZOP分析过程
1)定义目标与范围
定义HAZOP的研究目标应包括以下内容:
(1)评估节点最好在PID图上定义。
(2)评估时的设计状态,用定义PID版次状态来表示。
(3)影响程度和应考虑的邻近工厂。
(4)评估程序包括采取的行动和最终的报告。
(5)涉及对邻近或相关工厂的整体评估的准备。
2)分析准备
分析准备主要有资料准备、人员配备及进度计划等。
3)执行分析
HAZOP分析需要将工艺图或操作程序划分为分析节点或操作步骤,然后用引导词找出过程的危险,识别出那些具有潜在危险的偏差,并对偏差原因、后果及控制措施等进行分析。在考虑采取某种措施以提高安全性之前应对与分析节点有关的所有危险进行分析。
4)记录结果
HAZOP分析结果应精确地记录下来。负责人应确保有时间讨论汇总结果,应确保所有的成员知道并且对采取有关的措施形成一致意见。
5)措施跟踪
跟踪HAZOP进行整改是不可避免的。在某些适当的阶段,应对项目进行进一步的审查
3.F公司是存在危险化学品重大危险源,理由如下:S=q1/Q1+q2/Q2=8×40÷50+5×50÷50=11.4>1,构成了危险化学品重大危险源。
R=α(β1q1/Q1+β2q2/Q2)=2×(1×8×40÷50+1×5×50÷50)=22.8为三级重大危险源。
根据危险化学品种类的多少重大危险源的辨识分为以下两种情况:
(1)生产单元、储存单元内存在的危险化学品为单一品种时,该危险化学品的数量即为单元内危险化学品的总量(q),若等于或超过相应的临界量(Q),则定为重大危险源。
q/Q≥1
(2)生产单元、储存单元内存在的危险化学品为多品种时,按下式计算,若满足下式,则定为重大危险源:
S=q1/Q1+q2/Q2+...+qn/Qn≥1
S—辨识指标;
q1q2…qn—每种危险化学品的实际存在量,单位为吨(t);
Q1Q2…Qn—与各危险化学品相对应的临界量,单位为吨(t)。
危险化学品储罐以及其他容器、设备或仓储区的危险化学品的实际存在量按设计最大量确定。
危险化学品重大危险源分级
重大危险源的分级指标按照下式计算:

R—重大危险源分级指标;
α—该危险化学品重大危险源厂区外暴露人员的校正系数;
β1β2…βn—与每种危险化学品相对应的校正系数;
q1q2…qn—每种危险化学品实际存在量,单位为吨(t);
Q1Q2…Qn—与各危险化学品相对应的临界量,单位为吨(t)。
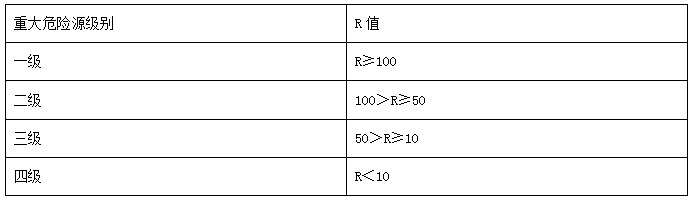
4.①查明事故发生的经过、原因、人员伤亡情况及直接经济损失;
②认定事故的性质和事故责任;
③提出对事故责任者的处理建议;
④总结事故教训,提出防范和整改措施;
⑤提交事故调查报告。
5.硫化氢属于既有毒又可燃的气体,对于既属于可燃气体又属于有毒气体的单组分气体介质,应设有毒气体探测器。
硫化氢分子量为34,与空气的比重为34÷29=1.17属于比空气略重的气体,检测比空气略重的可燃气体或有毒气体时,探测器的安装高度宜在释放源下方0.5m~1.0m。
基本要求
(1)在生产或使用可燃气体及有毒气体的生产设施及储运设施的区域内,泄漏气体中可燃气体浓度可能达到报警设定值时,应设置可燃气体探测器;
(2)泄漏气体中有毒气体浓度可能达到报警设定值时,应设置有毒气体探测器;
(3)既属于可燃气体又属于有毒气体的单组分气体介质,应设有毒气体探测器;
(4)可燃气体与有毒气体同时存在的多组分混合气体,泄漏时可燃气体浓度和有毒气体浓度有可能同时达到报警设定值,应分别设置可燃气体探测器和有毒气体探测器。
探测器安装高度要求
(一)一般规定
判别泄露气体和有毒气体介质是否比空气重,应以泄露气体介质的分子量与环境空气的分子量的比值为基准,并按下列原则判别:
(1)比值大于或等于1.2时,则泄露的气体重于空气。
(2)比值大于或等于1.0、小于1.2时,则泄露的气体略重于空气。
(3)比值大于0.8、小于1.0时,则泄露的气体略轻于空气。
(4)比值小于或等于0.8时,则泄露的气体轻于空气。
(二)探测器安装
(1)探测器应安装在无冲击、无振动、无强电磁场干扰、易于检修的场所,探测器安装地点与周边工艺管道或设备之间的净空不应小于0.5m。
(2)可燃气体或有毒气体探测器安装高度
检测比空气重的可燃气体或有毒气体时,探测器的安装高度宜距地坪(或楼地板)0.3m~0.6m;
检测比空气轻的可燃气体或有毒气体时,探测器的安装高度宜在释放源上方2.0m内。
检测比空气略重的可燃气体或有毒气体时,探测器的安装高度宜在释放源下方0.5m~1.0m;
检测比空气略轻的可燃气体或有毒气体时,探测器的安装高度宜高出释放源0.5m~1.0m。
(3)环境氧气探测器的安装高度宜距地坪或楼地板1.5m~2.0m。